Air Turbine Technology Inc., the leading manufacturer of revolutionary high-speed turbine products, highlights its new Air Turbine Spindles® 601 Series Spindle. This innovative spindle combines constant high speed in cut, energy efficiency and a user-friendly design. As a result of its governed high-speed performance, the 601 Series is an invaluable addition to any CNC magazine to accelerate productivity and reduce costs in today’s fast-paced industrial landscape
The compact 601 Series Spindle incorporates Air Turbine Technology Inc.’s patented governor technology, which increases CFM airflow on demand to maintain constant speeds of 40,000 to 90,000 RPM under cutting load on the toolpath through the program.
The 601 Series Spindle provides up to 0.2 HP (0.15 kW) power, delivering ample power for micro-machining applications – although Air Turbine Technology Inc.’s range includes spindles with power to 1.4HP (1kW) for larger tools and hard materials.
New features and improvements
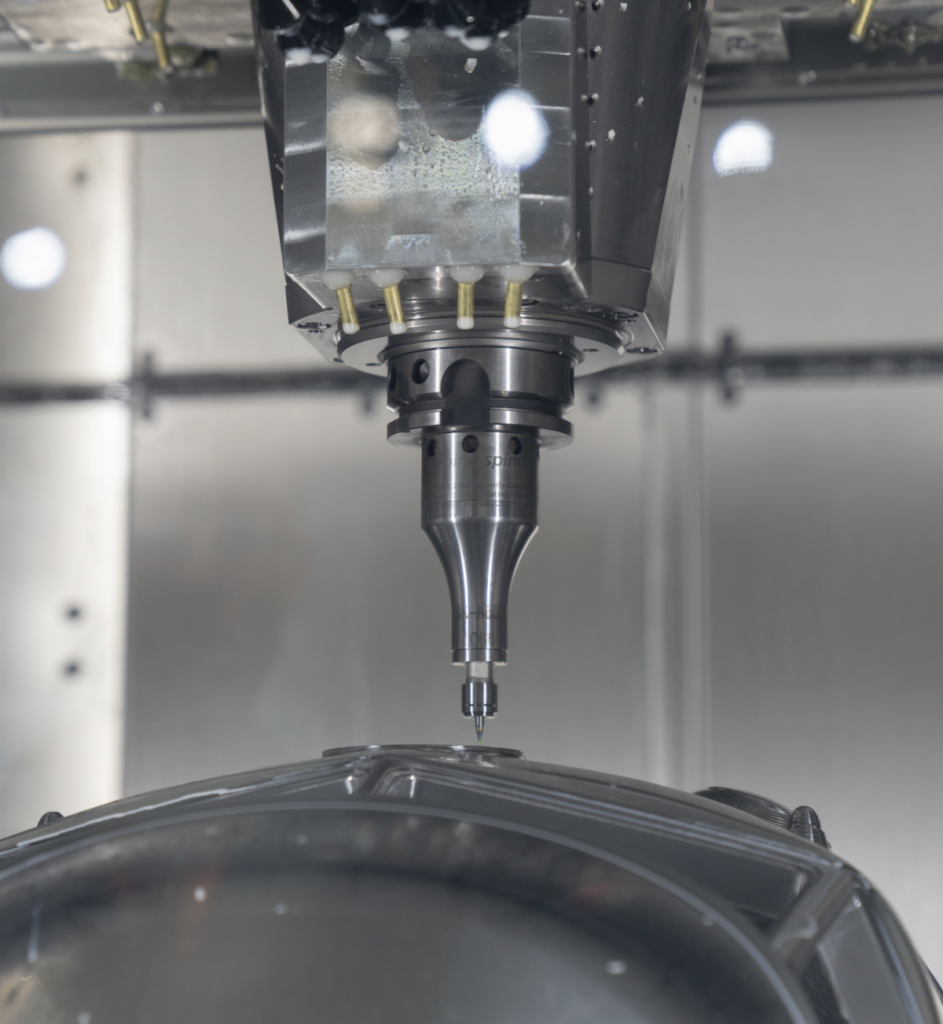
This unique governed turbine maintains the required surface feet per minute (SFM) and chip load for micro and small tools by sustaining high RPM on the toolpath.
Cycle Times are routinely reduced 6 to 10 times compared to standard CNC spindles at 6,000 RPM to at most 20,000 RPM. Maintaining high speed in cutting also optimizes tool performance, eliminating tool breakage and ensuring the production of standardized high-quality parts.
Air Turbine Technology Inc.’s direct drive 601 spindle generates no heat, delivering consistent 2-micron accuracy with no thermal growth in the spindle. No maintenance is needed and just 2 moving parts make this high-speed spindle reliable.
A connection to 90 psi (6.2 bar) air is all that is required to make any CNC a high-speed machine. Fully automated loading is available using air supply through the machine spindle, a collar and stop block or manual connection through the side air inlet. Easy installation minimizes downtime, allowing manufacturers to quickly adapt to changing production demands.
All benefits of the 601 Air Turbine Spindle
The high-speed capabilities of the 601 Air Turbine Spindle® streamline production by the elimination of secondary operations. Moreover, microtools are expensive. Big savings result from the optimization of small tool performance and life. Governed high speed also enhances the overall surface quality of the finished products.
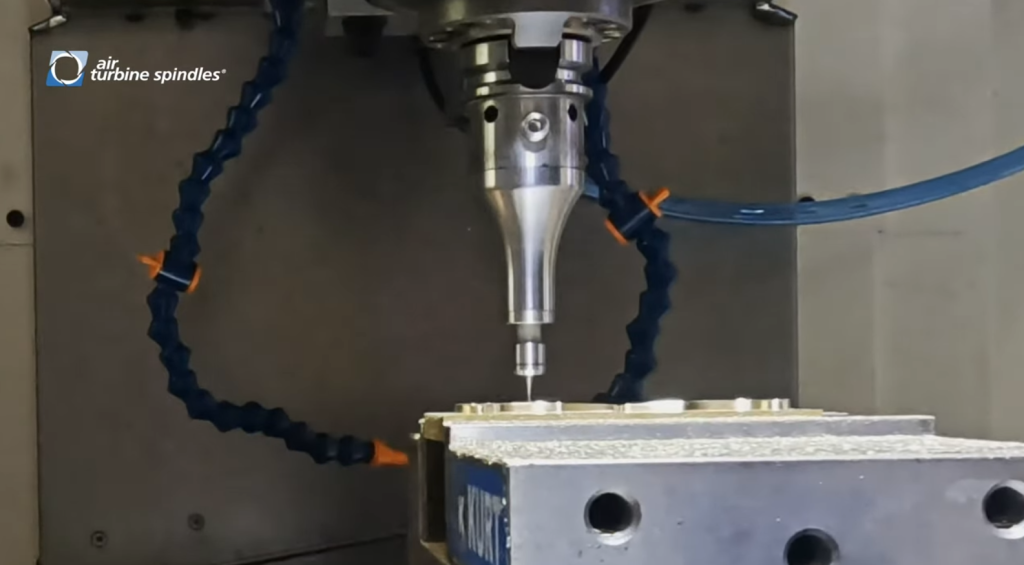
The 50 mm extended barrel on the 601 Series reaches into tight workpiece operations allowing greater maneuverability and access to pockets, angles and hard-to-reach areas. These dimensions enhance access and tool performance on all machines, including those with limited Z-Axis travel as well as 360˚5-Axis programming. Another great advantage is that the 601 design eliminates the need for long cutting tool stick-out from the spindle collet in angles or pockets causing vibration, tool breakage and poor surface quality.
Precision is paramount in the 601 Series Spindle design. Notably, Air Turbine Spindles® generate no heat, ensuring consistent accuracy during extended use. Operation with no heat also eliminates the need for a duty cycle, allowing continuous 24/7 operation without requiring cool-down periods. No lubrication is required in this high-speed turbine – eliminating contamination of parts from misting. This feature is especially important to the medical and food industries. The oil-free operation also reduces maintenance and lubrication costs.
Most popular taper options are available, including HSK-A63, CAT40, BT40, BT30, DIN30, DIN40, and 20mm JS straight shank enabling flexible use with any spindle taper.