The introduction of a new feed line for handling high thicknesses in cold sheet metal stamping, supplied by Asservimenti Presse, has enabled Tecnopress to improve efficiency and quality, offering new opportunities for growth
The increasing adoption of automation in production processes represents an important lever that companies cannot escape. This is to maintain competitiveness and free up valuable resources, lighten operators’ tasks, and respond to new market dynamics. Although there are cases where evolution is not always possible due to the type of business or production, it is equally true that making targeted choices can offer interesting growth opportunities to expand production capacity and set the pace for future development.
In this context of transformation, the case of Tecnopress emerges, operating in the field of metal carpentry and cold sheet metal stamping, metal welding, and mould construction and maintenance. The company has embarked on a significant path of technological innovation and generational change, culminating in the adoption of automated process solutions. These include the one provided by Asservimenti Presse of Massalengo (LO), which specialises in the production of systems for the automation of presses, reels, straighteners, electronic feeders and systems for complete sheet metal processing. This strategic choice demonstrates how automation can be the key to optimising production efficiency and guaranteeing high-quality standards.
Ready for stamping, ready to deform sheet metal
Tecnopress was founded in 1983 in Novellara (RE) from the experience in the mechanical sector of Enrico Cantarelli, assisted by his wife Anna. Later on during the early 1990s, their sons Massimo and Barbara continued the activity by introducing new processes and services, always under the banner of operational continuity. This continuity was aimed at customers who needed customised metal assemblies for every need, mainly belonging to the agricultural sector, a sector that has historically generated a very important local industry.
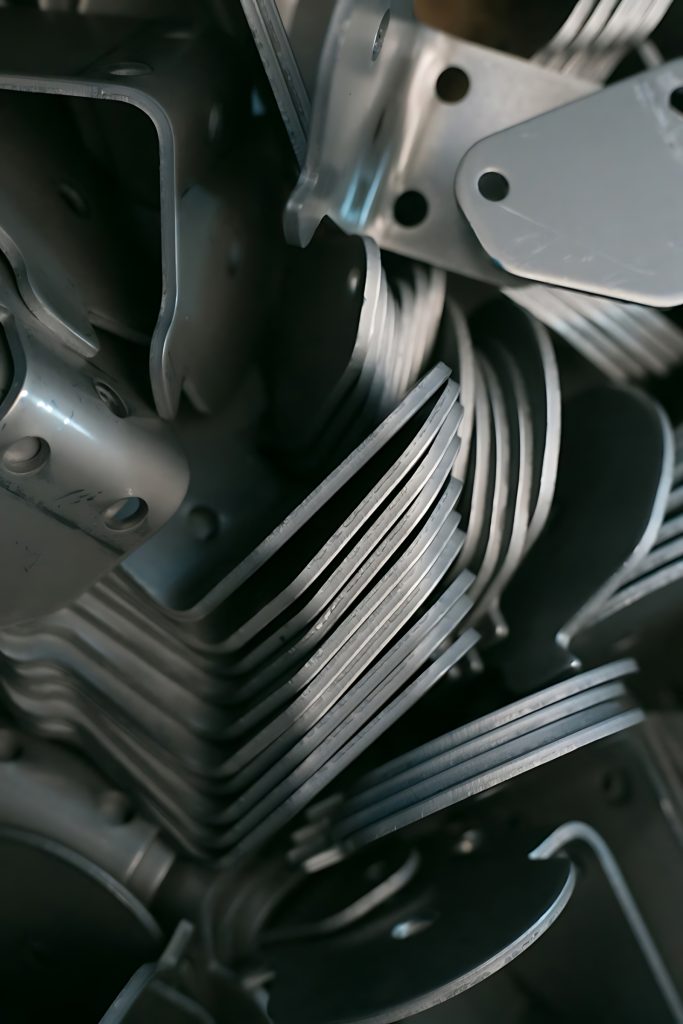
«Many of our customers – confirms Barbara Cantarelli – are tractor and handling machine manufacturers, to whom we supply all the medium-light carpentry part by stamping, or manufactured articles that we now supply cut and bent. This is why we can produce a wide range of products such as crankcases, welded frames, but also seats, brake units and steering columns».
In addition to the agricultural sector, which accounts for around 80% of the turnover (which stood at just over EUR 4.5 million last year), the company now also serves other markets.
«Where there is carpentry and the need to deform sheet metal – Cantarelli continues – we can make an important contribution. Especially in recent years, thanks to the crisis that has been occurring on and off, we have started to diversify more and more both our customers and the sectors we serve. Among these, for example, food stands out more and more strongly, as well as construction, to be understood in its broadest sense».
Production technologies
Tecnopress operates on an area of 15,000 square metres divided into three plants: one dedicated to laser cutting, bending and stamping; one to welding, tacking and assembly; and a third used as a warehouse for storing equipment and semi-finished products. About 30 employees work in the departments, including personnel for internal logistics and shipping.
In the cutting department, there is a 3-kW fibre laser technology plant, working area up to 1,500 x 3,000 mm, complete with an automatic loading/unloading system (cutting up to 15-20 mm), flanked by a 170-ton press brake, with a bending length of 3,050 mm. For cold forging, there are 22 presses from 30 to 400 tons, with working tables up to 1,000 x 1,500 mm. Since the early 1990s, the company has also introduced a welding in-house department, initially with manual workstations, later evolving robotic processes.
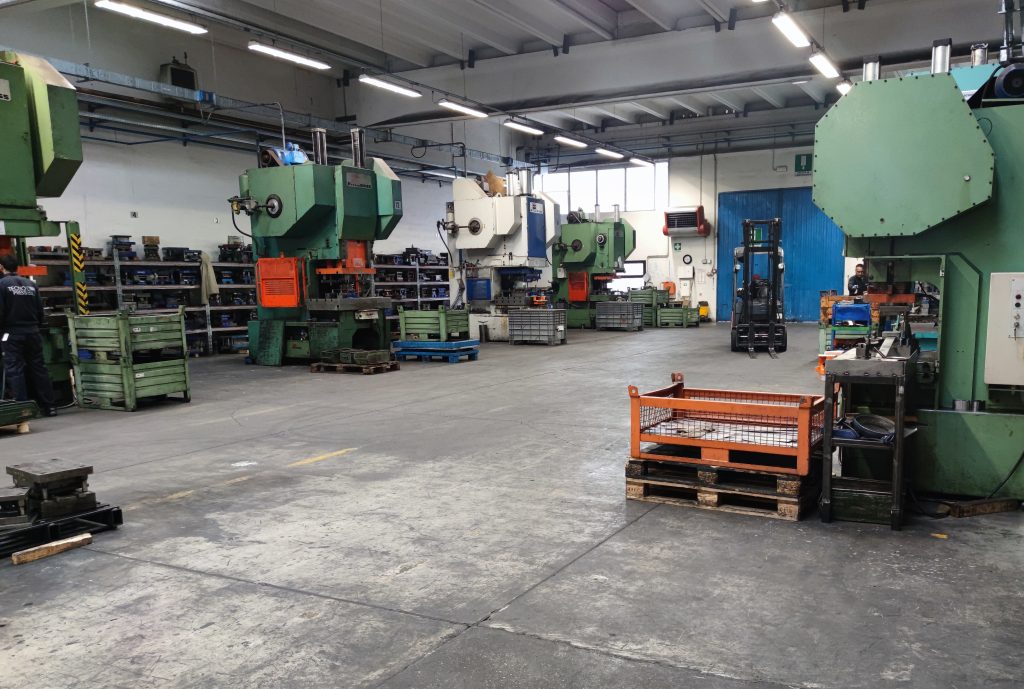
«Today we have 7 robotic welding islands with a double table – Cantarelli explains – one of which has a double arm, which allows us to produce with double jigs, optimising time and costs. Masks that we produce in our tooling shop, where we also carry out mould maintenance thanks to flexible lathes, machining centres and CNC milling machines».
The machine park available in the tool shop is very varied, necessary to quickly manage mould maintenance and give continuity to production, with a priority focus today on moulding.
«For the construction of large or particularly complex moulds – adds Cantarelli – we rely on specialised qualified partners, to offer an even higher quality service on our design. We can complete the production cycle with painting or galvanic treatments using established suppliers. Our machinery fleet allows us to act in a very flexible manner, guaranteeing maximum speed in deliveries».
Flexibility and organisation for complex projects
ISO 9001:2015 and UNI EN 1090 certified, Tecnopress offers an optimal size and structure to guarantee great flexibility and rigorous organisation, allowing it to act as a prime contractor for the supply of highly complex products. «We have the skills, tools and expertise – Cantarelli emphasizes – the result of more than four decades of experience, more than 2,500 sheet metal moulds made in-house or to our specifications, to take on an entire project. We can oversee the entire development cycle, from the design to the construction of the tooling, up to the optimisation and execution of production, to prevent non-conformities or resolve any criticalities that may arise during work. This means providing rapid responses: in 24 hours we can generate a quote and in 5 working days, thanks to a well-stocked warehouse, fulfil an order from the executive point of view».
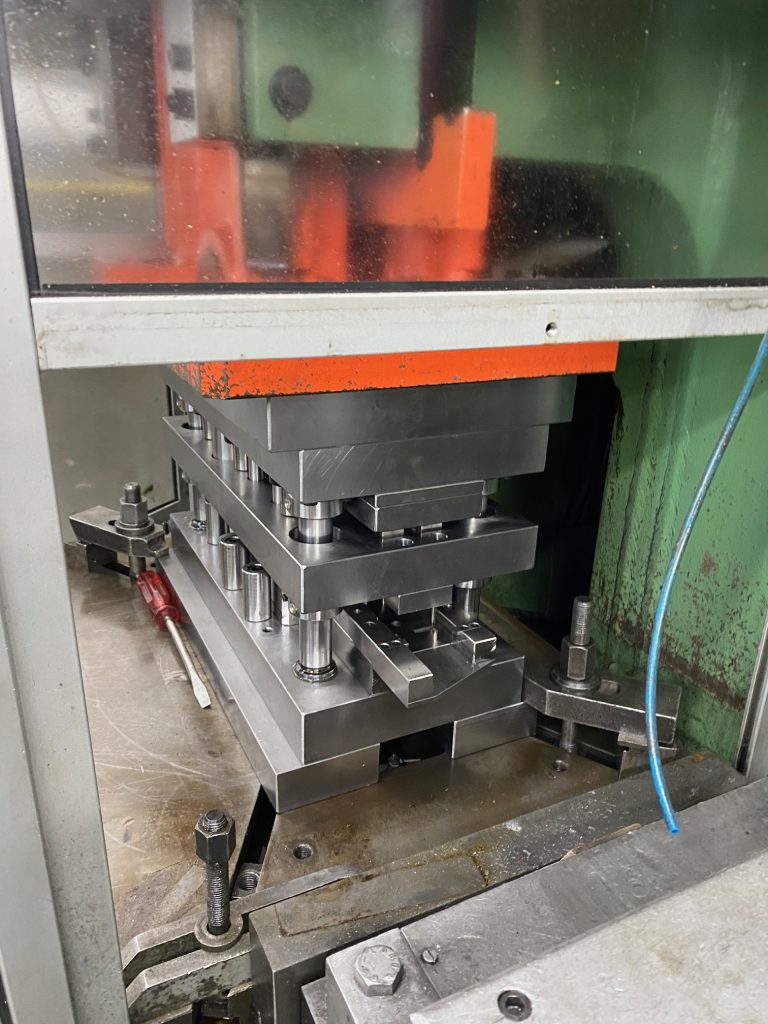
The company can process materials ranging from the most traditional, such as S235 and S355 steels, stainless steel in its different varieties, to less typical ones such as brass, copper aluminium and, in some cases, even non-ferrous materials. With the technology at its disposal, it can produce samples from 1, 5, and 10 pieces, up to batches that can reach and exceed 30,000 units, but with a production capacity that is twice as high. «Over the years – adds Cantarelli – for some of our customers, we have organised ourselves to guarantee and manage supplies with a Kanban system. Today, batches are much more fragmented than in the past, with more frequent deliveries. Also, from this point of view, we can manage orders and deliveries following customer-specific methodologies and information flows, thanks to an adequate and evolved IT infrastructure. This is based on management software interconnected with all production machines, with the possibility of real-time monitoring of the progress».
High flexibility on all thicknesses
Presiding over the design and technological development activities at Tecnopress today is Pietro Galeazzi, the third generation in the company, who is called upon to interface with both production and the quality department. It is also his important contribution to the decision to implement new automated solutions.
«As management – says Cantarelli – I had given input to verify and identify new opportunities to increase production capacity, to decrease tooling times and man-machine control».
But it was above all a precise technological need that guided the investment decision.
«The need – explains Galeazzi – was to be able to automatically process what, for our stamping production, represent the high’ thicknesses, i.e. 4, 5, 6 mm sheets».
After a careful evaluation of the solutions available on the market, with the support of funds granted by a regional call for tenders on process digitisation, the company chose to invest in an integrated system supplied by Asservimenti Presse: an Smc 50 type reel complete with a CRM AP 400 C H model straightener. This decision was the result of a selection process that took into account not only the technical performance of the system but also factors such as the reliability of the supplier and delivery and installation times.
«Another decisive aspect – adds Galeazzi – was the ability of Asservimenti Presse to provide a system that could adapt to the available, geometrically constrained space without compromising performance or providing for a displacement of the press».
Consistent quality and process repeatability
The implementation of the new system has led Tecnopress to a significant improvement in its operational capabilities. The system is characterised by its remarkable versatility, being able to handle coils with a diameter of up to 1,500 mm and a width of up to 400 mm, with a range of thicknesses from 0.7 to 6 mm, on a 400-ton press. This flexibility is an important competitive advantage, allowing the company to respond effectively to different production requirements. The motorised adjustment of the straightening unit adds a further element of versatility to the system, ensuring greater adaptability to different working configurations.
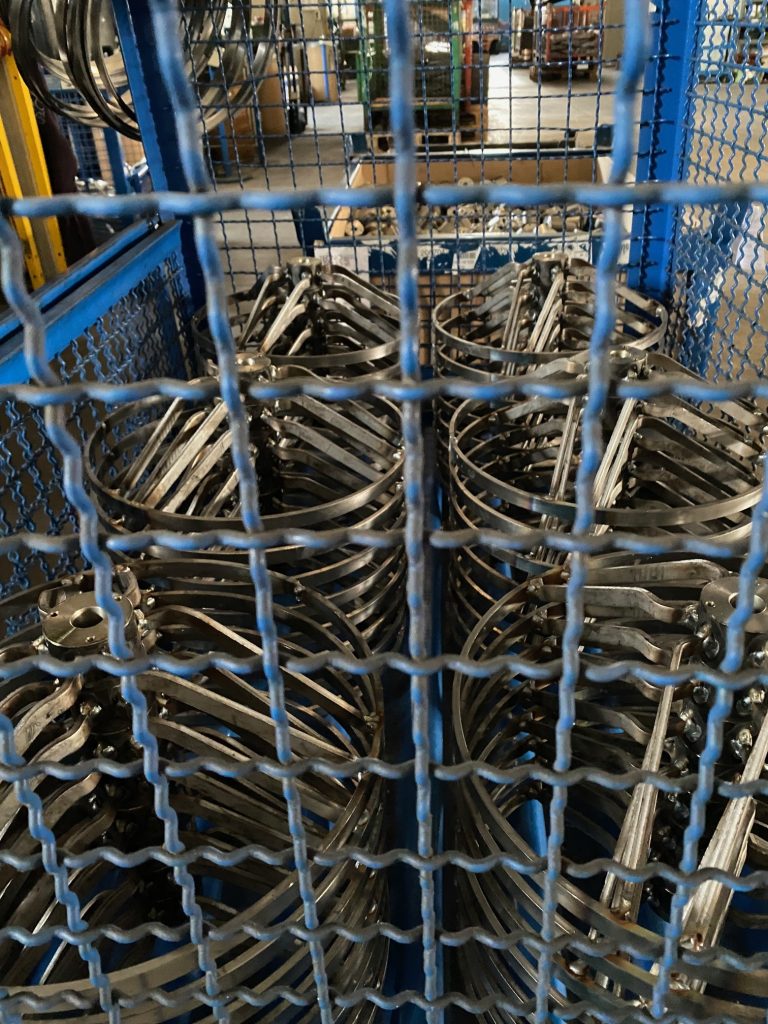
«A relevant aspect of the implemented automation – Galeazzi emphasizes – concerns the constant quality standards and process repeatability. While the process speed is much higher than with manual handling, it is above all the certainty of constant quality and repeatability that represents the real added value. The elimination of the variables associated with manual intervention has made it possible to optimise production times and guarantee high and consistent quality standards without supervision. This aspect is important in the safe machining of high thickness, where precision and repeatability are critical factors for the quality of the final product». Automation has also reduced set-up and production changeover times, contributing to an overall increase in efficiency. The ability to automatically handle thicker materials has also opened up new market opportunities, allowing the company to expand its service offering.
The impact on production and new opportunities
The introduction of the new automated system has also stimulated a profound revision of existing processes at Tecnopress.«The biggest challenge – admits Galeazzi himself – thanks to the availability of this new production line, is now to readapt many historical productions».This optimisation process has led to a complete rethinking of some processes that previously required the use of 5-6 moulds, allowing them to be carried out with fewer steps and, consequently, a significant reduction in production time and costs. The optimisation process was not limited to the simple automation of existing operations but involved true re-engineering of production processes. In this sense, the Tecnopress technical team started a systematic re-evaluation of existing equipment, trying to identify opportunities for improvement and optimisation.
Training, prospects and sustainability
Tecnopress showed great appreciation for the Lodi-based manufacturer’s ability to meet delivery and installation deadlines.
«Both during testing and start-up – Barbara Cantarelli emphasizes – the support of the Asservimenti Presse technicians was commendable. This was also confirmed by our operators, who came from several foreign countries and received clear and comprehensive training».
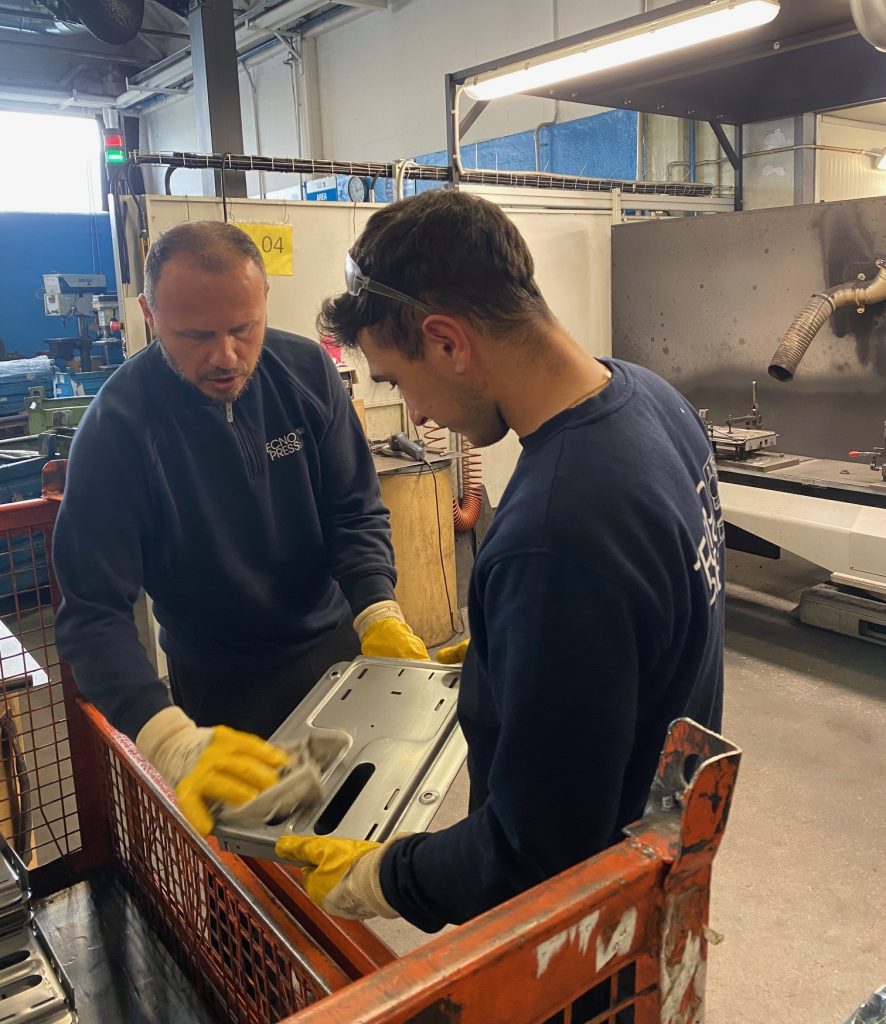
The training was not only limited to the start-up phase but also continued with after-sales support that further optimised the use of the system. As already stressed, the integration of the new plant is part of a broader strategic vision that looks to the future of the company.
«I see in the future – Pietro Galeazzi concludes – a much more structured Tecnopress at the level of industrial automation. I see operators who are competent and relieved of their heaviest tasks, and who are given tools that are in step with innovation».
This vision is accompanied by a strong focus on sustainability issues, considered not only as a regulatory obligation but as a real opportunity to create value. Automation is therefore seen by Tecnopress as a tool for achieving environmental and social sustainability objectives, allowing the optimisation of resource use and improving working conditions.
Efficiency and versatility for different material thicknesses
The feeding line supplied to Tecnopress by Asservimenti Presse consists of a motorised decoiler and a feeding straightener, serving the processing of steel from 0.7 to 6 mm thick. The decoiler is designed to handle coils up to 5,000 kg with a mandrel expansion of 470 to 550 mm and a maximum outside diameter of 1,500 mm. Its speed of 10 rpm enables stable and efficient material feeding, thanks also to the centring system using a hydraulic cylinder and guided wedges, which ensure optimal positioning.
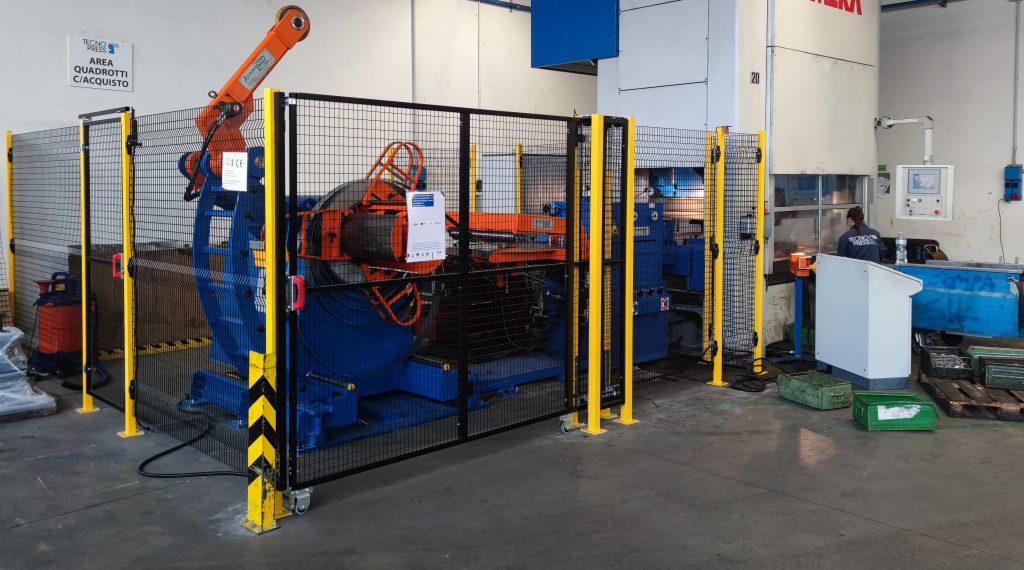
The integration of an adjustable clutch brake provides accurate torque control, while the hydraulic reel drive ensures perfect alignment. The feeder straightener, with a solid structure in cast iron and electro-welded steel, is equipped with 9 straightening rolls and 2 pinch rolls, all 100 mm in diameter. The self-centring device and pneumatic feed system facilitate the start of processing, while the upper head with folding opening facilitates maintenance. Brushless motorisation, managed by an advanced electronic control, allows the adjustment of pitches with absolute precision, responding dynamically to production requirements. The control panel makes operation intuitive and ensures continuous monitoring of functions. The loop control via ultrasound and photocells keeps the web tension constant, increasing the overall reliability of the line. Thanks to these innovative solutions, the system stands out for its efficiency, versatility and ability to adapt to different material thicknesses and strengths.